Modellierung der Spannungs-Dehnungs-Kurve zweiphasiger Stähle unter Berücksichtigung der Kornstruktur
Ansprechpartner
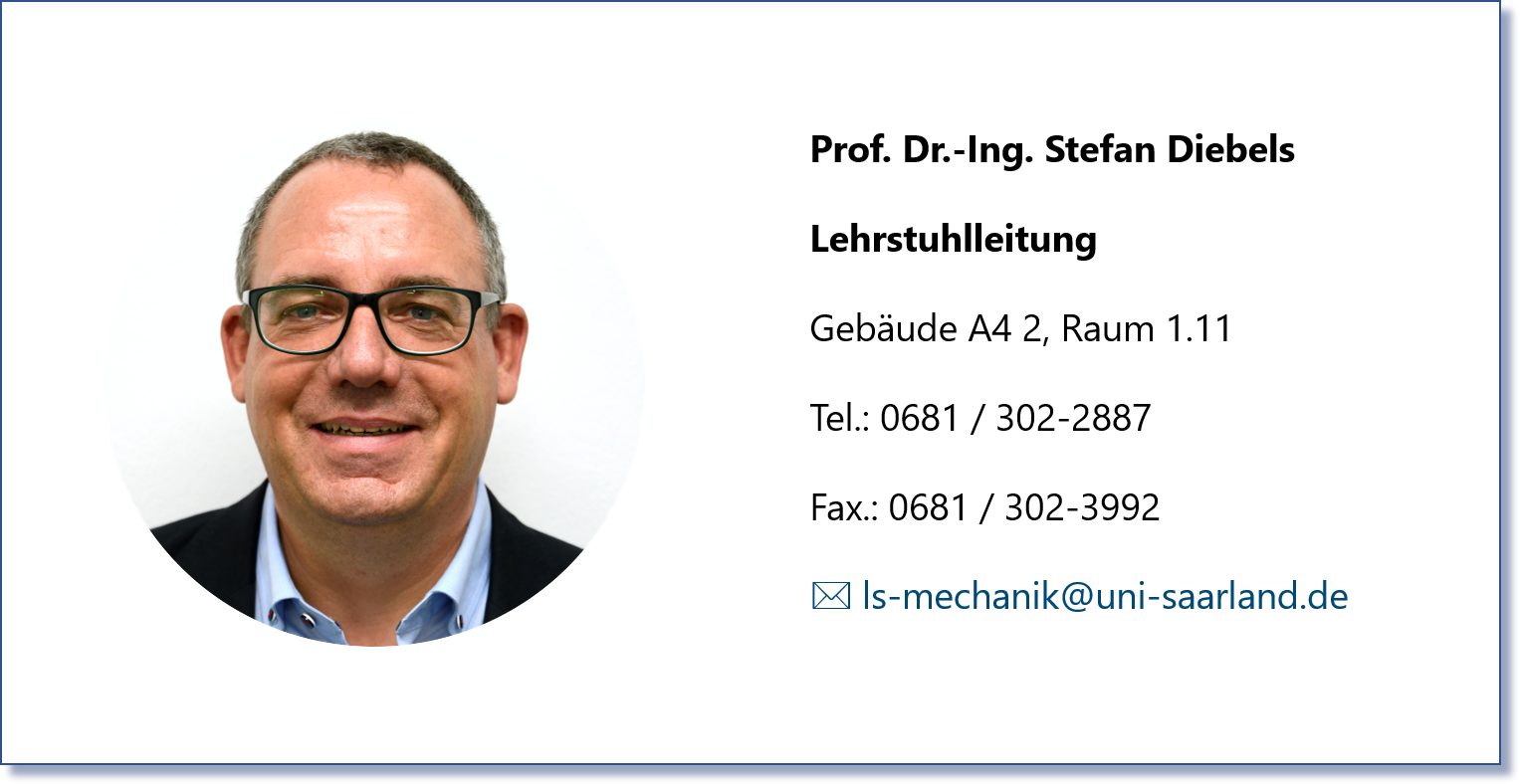
Projektträger

AG der Dillinger Hüttenwerke, Abteilung Grobblech-Forschung
Kooperationen
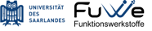
Prof. Dr.-Ing. Frank Mücklich, LS für Funktionswerkstoffe, UdS
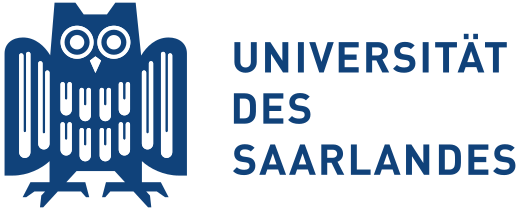
Prof. Dr. mont. Christian Motz, LS für Experimentelle Methodik der Werkstoffwissenschaften, UdS

Prof. Dr. Tobias Kraus, Strukturbildung, INM - Leibniz-Institut für Neue Materialien gGmbH
Projektbeschreibung
Das Ziel des Projekts ist die Vorhersage des mechanischen Verhaltens beliebiger Gefüge von Dualphasenstahl und Komplexphasenstahl schon vor Beginn des Produktionsprozesses. Zu diesem Zweck wird ein numerisches Modell zur Bestimmung des Deformationsverhaltens auf Basis der dreidimensionalen Mikrostruktur entwickelt und validiert. Fokus des Projekts liegt auf der Simulation des anisotropen Deformationsverhaltens aufgrund kristallographischer Vorzugsorientierungen (Textur) in der ferritischen Matrixphase. Dazu muss ein geeignetes Modell gefunden werden, das auf Mikroskala betrachtet die kubische Symmetrie des kubisch-raumzentrierten Ferrits abbilden kann und makroskopisch das anisotrope Fließverhalten korrekt vorhersagt. Ein weiterer Teil der Arbeit besteht darin, eine Methode zur Erzeugung einer virtuellen 3D Tomographie auf Grundlage möglichst weniger experimenteller 2D Daten zu entwickeln, die neben der Phaseninformation auch die Korngrößen- und Kornorientierungsinformation beinhaltet.
Dualphasen- und Komplexphasenstähle zeichnen sich durch ihre hohe Dehnbarkeit bei gleichzeitig hoher Festigkeit aus, die durch die Kombination aus weicher, gut verformbarer Matrix und härteren aber auch spröden Bereichen zweiter Phase erreicht wird. Aufgrund dieser hervorragenden Eigenschaften kommen diese Stähle in vielen Bereichen von Karosserieblech bis hin zu festigkeitsrelevanten Trägerstrukturen zur Anwendung. Die Herstellung dieser Stähle basiert bislang stark auf Erfahrungswerten. Um die Produktion effizienter zu gestalten ist eine prozessbegleitende Simulation erwünscht, die Vorhersagen über das mechanische Verhalten abhängig von der zugrunde liegenden Mikrostruktur erlaubt. Das mechanische Verhalten von Dual- und Komplexphasenstählen hängt zum einen von der Phasenstruktur und zum anderen von der Kornstruktur, insbesondere der der Matrixphase, ab. Durch den Walzprozess bei der Herstellung werden die Kristallite in der Matrix stark verformt und verdreht, sodass die anfänglich willkürlich verteilte Kristallorientierung in eine Orientierungsverteilung mit bevorzugten Richtungen übergeht und die Kristallite in Walzrichtung gestreckt werden. Dadurch wird das mechanische Verhalten dieser Stähle richtungsabhängig. Diese Anisotropie insbesondere im plastischen Verformungsbereich muss mit dem verwendeten Simulationsmodell abgebildet werden können.
Zur Modellierung anisotroper Plastizität werden in der Literatur im Allgemeinen zwei Hauptansätze vorgestellt. Kristallplastizitätsmodelle führen die plastische Verformung von metallischen Werkstoffen auf die Bewegung von Gitterdefekten im atomaren Metallgitter, sogenannten Versetzungen, zurück. Die Versetzungen bewegen sich dabei nur auf bestimmen Ebenen in bestimmte Richtungen. Ein System aus einer solchen Gleitebene und einer Gleitrichtung wird als Gleitsystem bezeichnet. In Kristallplastizitätsmodellen muss für jedes vorhandene Gleitsystem eine eigene Fließfunktion aufgestellt und ausgewertet werden. Im hier betrachteten kubisch-raumzentrierten Ferrit sind bis zu 48 Gleitsysteme pro Korn möglich. 24 davon sind allerdings sehr unwahrscheinlich und werden vernachlässigt. Insgesamt müssen damit 24 Fließfunktionen pro Korn ausgewertet werden. Damit sind solche Modelle bei großen betrachteten Volumina mit vielen Kristallen eines Polykristalls äußerst rechenintensiv. Der Einsatz in der Stahlindustrie erfordert jedoch eine möglichst kurze Rechenzeit. Dementgegen existiert eine Vielzahl makroskopischer Modelle, die dieser Anforderung gerecht werden. Diese makroskopischen Ansätze bestehen in der Formulierung einer einzigen makroskopischen Fließfunktion. Durch Auswertung der Fließfunktion lassen sich Spannungszustände einer makroskopischen Probe bestimmen, die zu plastischem Verhalten führen. Graphisch wird dies durch die sogenannte Fließfläche dargestellt.
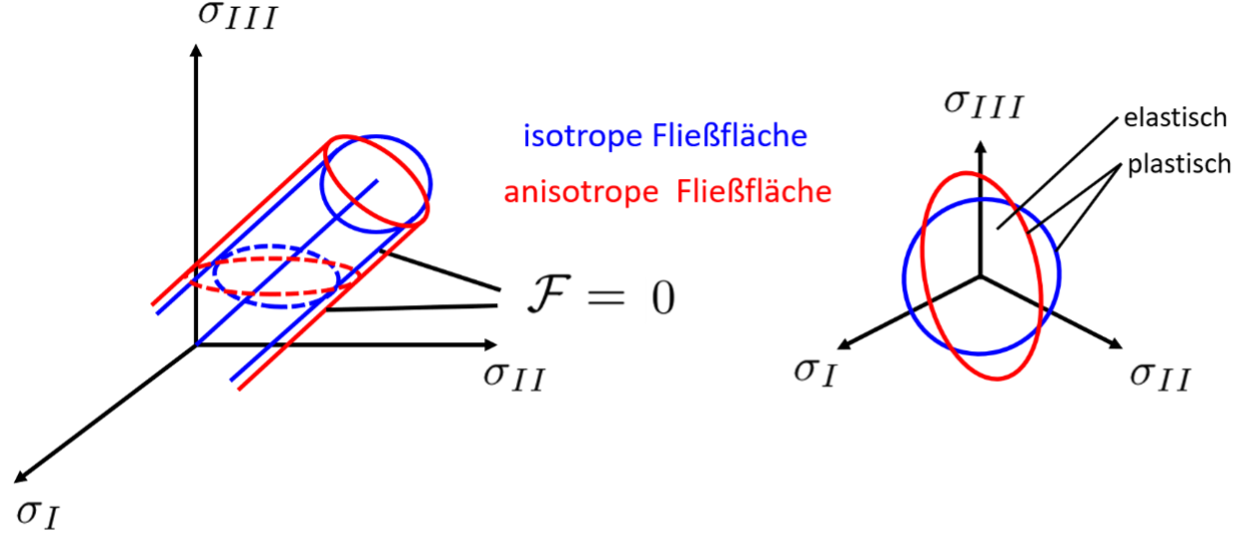
Abbildung 1 zeigt schematisch eine Fließfläche für ein isotropes und ein anisotropes Material. Alle Spannungszustände innerhalb der Fließfläche führen zu elastischem Verhalten. Sobald jedoch die Fließfläche getroffen wird, verformt sich das Material plastisch. Bei Isotropie ist der Fließspannungswert für Zug in I-, II- oder III-Richtung gleich groß, wohingegen bei Anisotropie in dem gezeigten Beispiel eine Probe bei Zug in I- und II-Richtung deutlich früher zu plastifizieren beginnt, als in III-Richtung. Die Modellparameter, die in der Fließfunktion stecken, werden durch Versuche an makroskopischen Proben ermittelt, sodass in solchen Ansätzen die Verformung makroskopisch durch eine Mittelung über alle vorkommenden Kristallite beschrieben wird.
Das Ziel dieses Projektes ist es daher, einen alternativen Modellansatz zu finden, der eine lokale, hochaufgelöste, mikroskopische Betrachtung der Verformung jedes einzelnen Kristallits mit einer möglichst kurzen Rechenzeit vereint. Um die rechenaufwändigen Kristallplastizitätsansätze zu umgehen, aber dennoch eine lokale Auflösung des Spannungs-Dehnungs-Verhaltens zu erreichen, wird eine Fließfunktion auf Kristallebene definiert, die im Folgenden als mikroskopische Fließfunktion bezeichnet wird. Der Rechenaufwand wird durch die Reduktion von 24 auf eine Fließfunktion deutlich verringert.
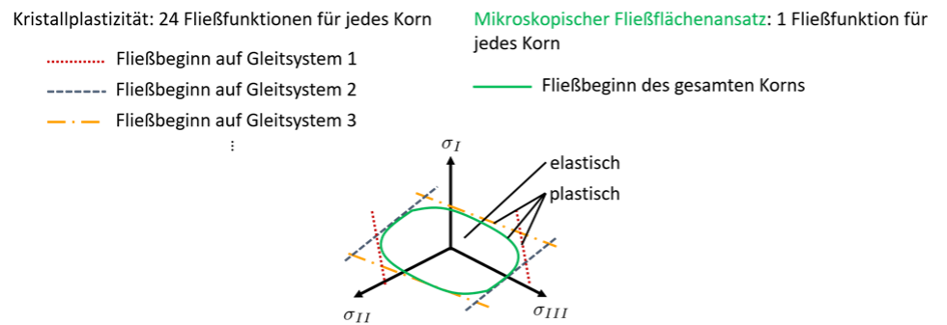
Die mikroskopische Fließfläche beschreibt abhängig von der jeweiligen Kristallorientierung die Richtung und das Ausmaß der Verformung für jeden einzelnen Kristalliten und erlaubt daraus die Verformung der makroskopischen Probe, ohne auf eine Mittelwertberechnung zurück zu greifen, zu errechnen. Durch die Reduzierung der Rechenzeit bei ähnlicher Genauigkeit im Vergleich zu Kristallplastizitätsmodellen kann das Modell im industriellen Rahmen die Wirtschaftlichkeit bei der Erzeugung neuer Stahlgüten deutlich verbessern, da der bislang auf Erfahrungswerten aufbauende, iterative Prozess durch die Simulationen unterstützt und verkürzt werden kann. Dabei können Ressourcen geschont werden, da die Gefahr der Produktion eines Bleches mit unzureichender Qualität drastisch reduziert wird.
Um die Simulation durchführen zu können, bedarf es aber einer dreidimensionalen Mikrostruktur, die Informationen über Form, Größe und Orientierung der Körner im Polykristall beinhalten muss. Diese Mikrostruktur wird für die Simulation in ein finites Elemente Netz zerlegt. Dann können verschiedene Randbedingungen aufgebracht und die Simulation unter Verwendung des zuvor entwickelten Materialmodells durchgeführt werden. Die experimentelle Erzeugung eines dafür notwendigen 2D-Bilderstapels ist allerdings sehr aufwändig und zeitintensiv. Daher besteht der zweite Projektteil darin, ein Verfahren zu entwickeln, mit dem solche Mikrostrukturen realitätsnah auf Grundlage von möglichst wenigen experimentellen Daten virtuell erzeugt werden können. Dazu werden die Korngrößenverteilung und insbesondere die Aspekt-Verhältnisse der Körner statistisch aus je einer Lichtmikroskopaufnahme einer Ebene senkrecht zur Normalenrichtung, senkrecht zur Walzrichtung und senkrecht zur Querrichtung bestimmt. Zudem ist zur Bestimmung der Orientierungsdichteverteilung eine EBSD-Messung des Materials notwendig. Diese Daten werden zur Erzeugung der virtuellen Mikrostrukturen in die quelloffene Software DREAM.3D eingelesen und dort die resultierende virtuelle Mikrostruktur erzeugt.
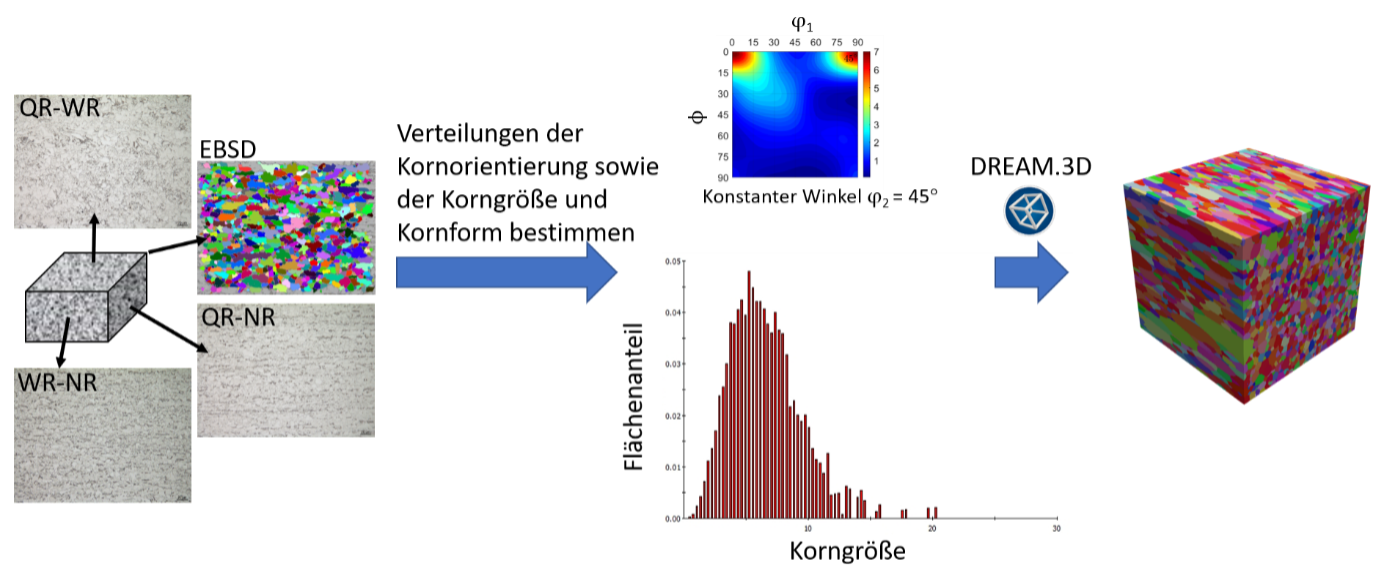