Simulation und qualitätsabhängige Optimierung von Scherprozessen
Kontakt
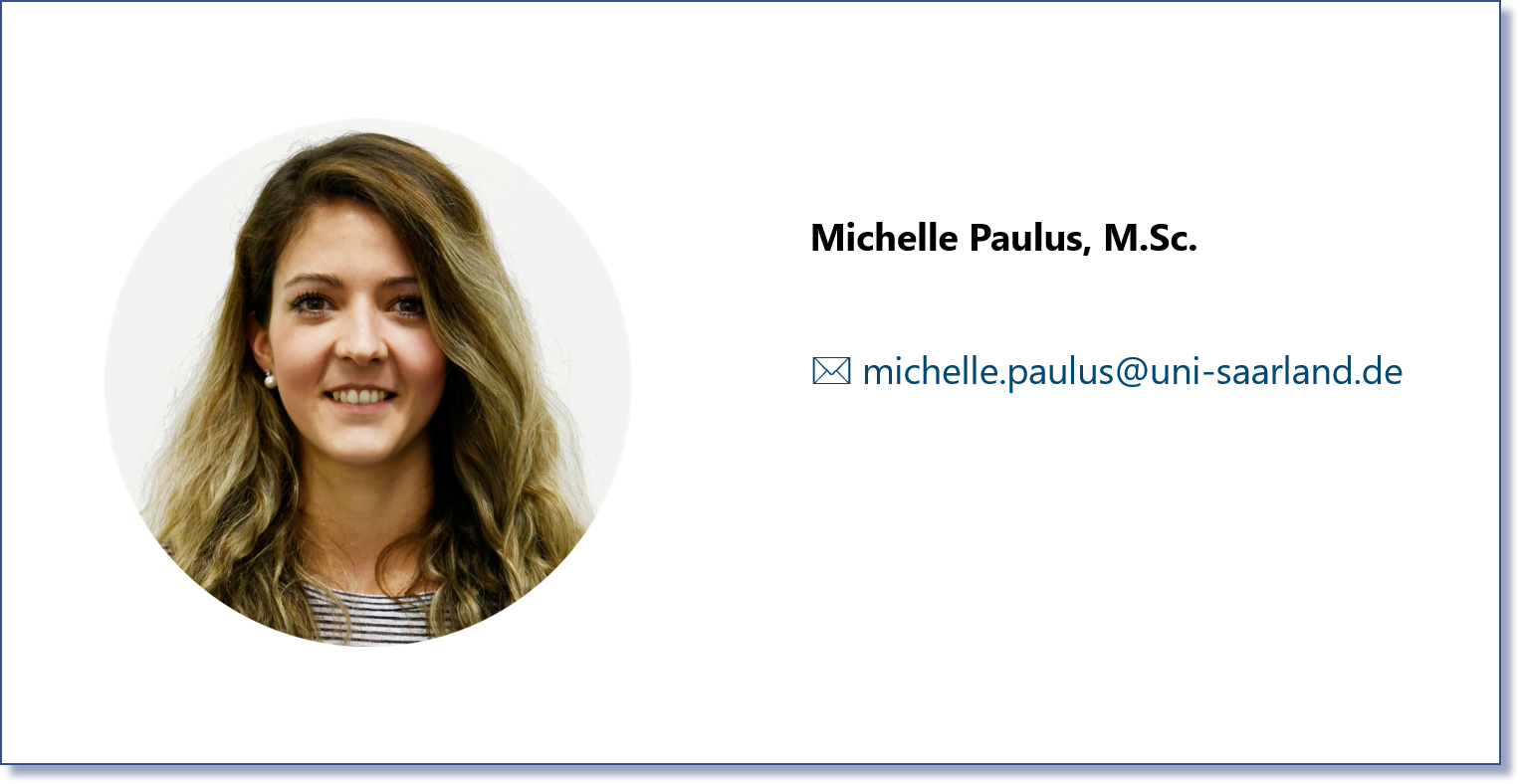
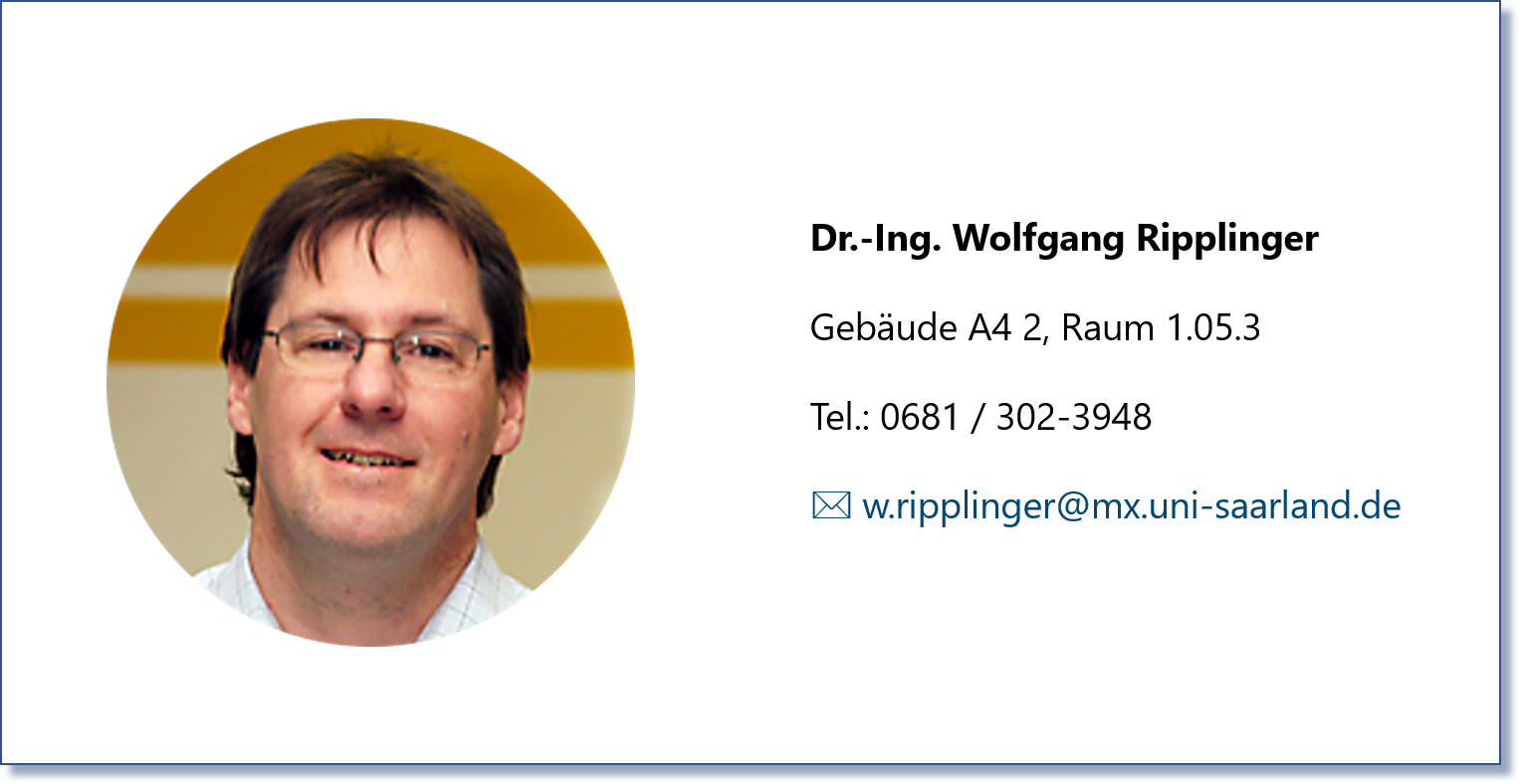
Projektträger

AG der Dillinger Hüttenwerke, Abteilung Technologie Walzwerk
Projektbeschreibung
Die AG der Dillinger Hüttenwerke produziert Bleche, die bis zu 450 mm dick, bis zu 5,2 m breit und bis zu 28 m lang sein können. Die Herstellung solcher Bleche ist technologisch anspruchsvoll: vom Stahlwerk gelieferte Brammen werden zunächst erwärmt, bevor sie zu sogenannten Walztafeln gewalzt und wieder auf die geforderte Temperatur abgekühlt werden können. Es folgen in der Regel verschiedene Wärmebehandlungen, um die gewünschten Materialeigenschaften zu erzeugen. Abschließend werden die Tafeln auf ein kundenspezifisches Endmaß zugeschnitten.
Aus Gründen der Zeiteffizienz erfolgt dieser Zuschnitt bevorzugt auf mechanischen Scheranlagen. Mechanische Scherverfahren führen jedoch häufiger zu Defekten an den Schnittflächen der Bleche, die aufwendig nachbearbeitet werden müssen (Abbildung 1).
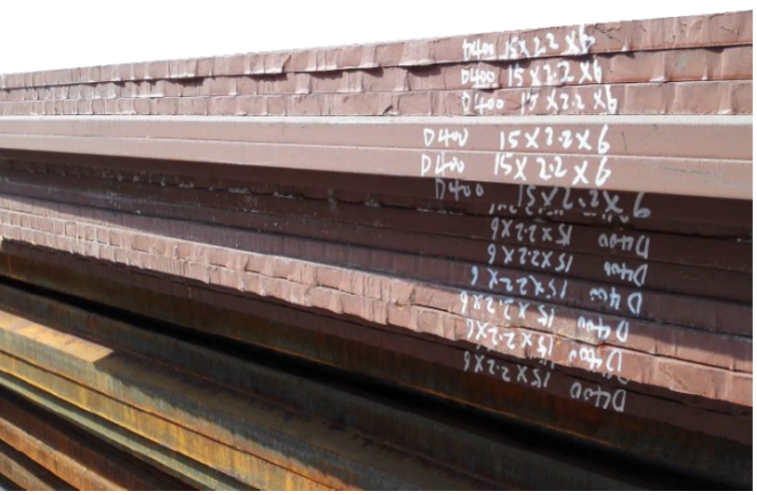
Um solche Nachbearbeitungsprozesse zu vermeiden, werden die Bleche vorab auf ihre mechanische Scherbarkeit überprüft. Bis zum heutigen Zeitpunkt basiert diese Beurteilung auf empirisch ermittelten Daten, welche nach dem Trial-and-Error-Prinzip über umfangreiche Versuchskampagnen an den Scheren erhoben werden. Diese Vorgehensweise ist nicht nur zeit- und kostenintensiv, sondern bietet insbesondere auch keine Möglichkeit zur systematischen Analyse und Verbesserung des Scherprozesses. So bleibt z. B. der Einfluss des zu scherenden Materials auf die Ausprägung der Schnittkanten unklar.
Dieses Projekt befasst sich daher mit der Entwicklung eines Finite-Elemente(FE)-Modells des Scherprozesses. Damit soll
- eine Vorhersage der Schnittkantenqualität und
- eine systematische Analyse und Optimierung des Scherprozesses
in Abhängigkeit des zu scherenden Materials und ohne die Durchführung aufwendiger Versuchskampagnen ermöglicht werden.
Die Entwicklung eines solchen FE-Modells beinhaltet zunächst die Definition der Geometrie und die Formulierung von geeigneten Randbedingungen, die den realen Scherprozess in der gewünschten Genauigkeit abbilden. Da der Fokus des Projekts auf den materialabhängigen Einflussfaktoren liegt, wurde der Guillotinenschnitt als kinematisch einfacher Scherprozess modelliert (Abbildung 2).
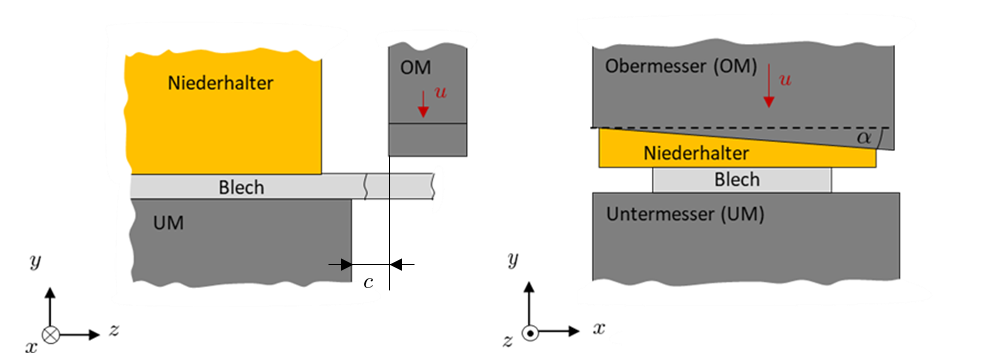
Verwendet wurde die kommerzielle FE-Software Abaqus®. Das Modell besteht aus
- einem unbeweglichen Untermesser(UM), auf dem ein 15 mm dickes Blech aufliegt,
- einem beweglichen Obermesser(OM), das um den Schnittwinkel abgeschrägt ist
- und einem Niederhalter, der ein Verkippen des Blechs während des Scheren verhindert.
Das Abtrennen des Schrottstreifens vom Blech geschieht durch eine geradlinige Abwärtsbewegung des Obermessers um die Verschiebung . Der horizontale Abstand zwischen Ober- und Untermesser (Scherspalt ) beträgt 1,5 mm. Es wurde eine Schnittgeschwindigkeit von 3 m/s identifiziert, sodass sich der Prozess gerade noch im quasistatischen Bereich befindet und dynamische Effekte ausgeschlossen werden können. Die Deformation der Werkzeuge wird als vernachlässigbar gering eingestuft.
Neben der Definition der Geometrie und der Formulierung geeigneter Randbedingungen wird zudem ein Materialmodell benötigt, welches das Materialverhalten in ausreichender Genauigkeit abbilden kann. Eine große Herausforderung stellt dabei die Modellierung des Schädigungsverhaltens dar. Hierfür wurde zunächst der Belastungszustand des Blechs anhand der Spannungstriaxialität während des Scherprozesses analysiert (Abbildung 3).
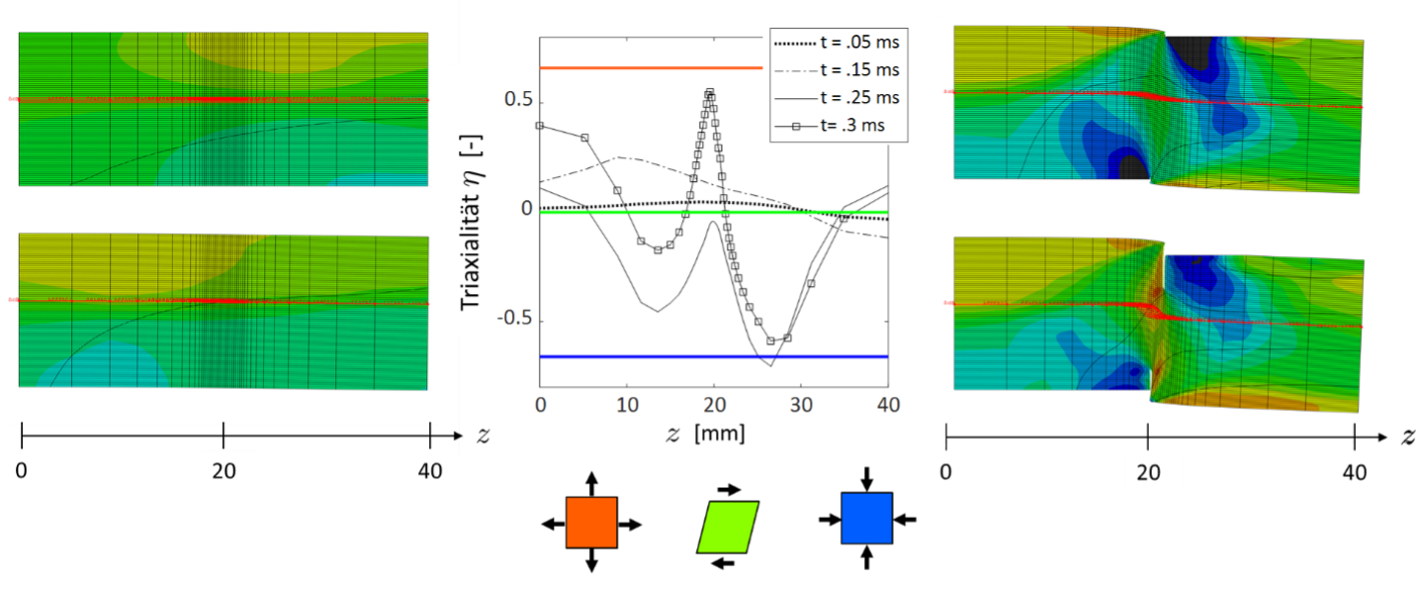
Der Triaxialitätsverlauf verdeutlicht, dass das Material während des Scherens einer sich ändernden multiaxialen Belastung unterliegt. Bei ähnlichen Belastungsfällen aus der Literatur konnten gute Ergebnisse durch die Berücksichtigung der Spannungstriaxialität im Materialmodell erzielt werden. Das (vereinfachte) elastisch-plastische Schädigungsmodell nach Lemaitre bietet eine Möglichkeit, die Spannungstriaxialität in der Schädigungsentwicklung zu berücksichtigen. Eine leicht abgewandelte Form dieses Modells wurde daher über die Abaqus® User-Subroutine VUMAT implementiert. Erste Simulationsergebnisse zeigen, dass mit der Implementierung des Lemaitre-Modells deutliche Effekte des Scherprozesses an der Schnittkante zu sehen sind.
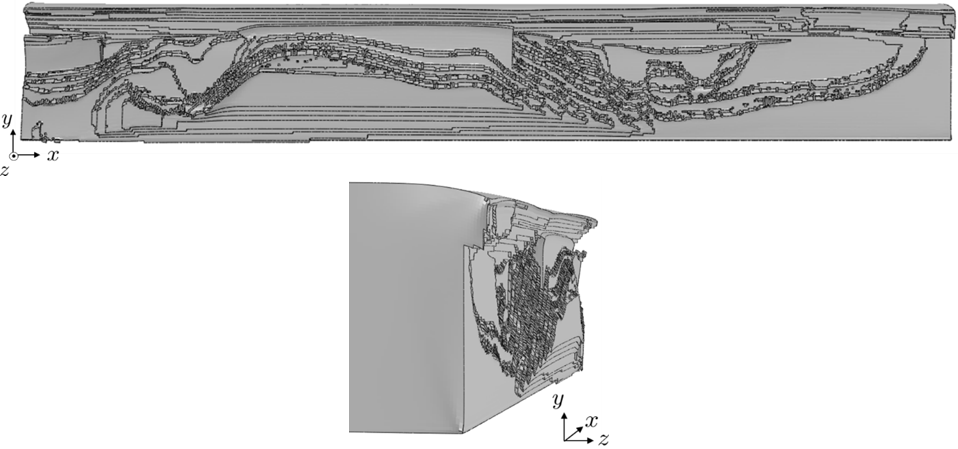
Das Materialmodell muss jedoch nicht nur geeignet mathematisch formuliert werden, sondern auch mit entsprechenden Experimenten kalibriert und verifiziert werden. Im Rahmen der Verifizierung ist insbesondere der Abgleich zwischen berechneten und realen Schnittkanten wichtig. Daher wurden Scherversuche an einer Guillotinenschere durchgeführt.
Unmittelbar vor Versuchsbeginn wurden die Messer gewechselt, sodass ein definierter Messerzustand vorlag. Es wurden vier unterschiedliche Blechmaterialien geschnitten, die erfahrungsgemäß unterschiedliche Schnittkantenergebnisse (gut – neutral – schlecht) liefern. Jedes Material wurde bei jeweils drei unterschiedlichen Scherspalteinstellungen (klein – normal – groß) geprüft. Anschließend wurde die Oberflächenstruktur der Schnittkanten dreidimensional rekonstruiert. Für die 3D-Rekonstruktion wurde die Oberflächenstruktur mit einem Gemisch aus Wasser, weißer Dispersionsfarbe und Spülmittel sukzessive geflutet. Die Flutung und die damit einhergehende Inselbildung wurde über eine Kamera aufgezeichnet, die senkrecht über der Schnittkante angeordnet wurde (Abbildung 5).

Das aufgezeichnete Bildmaterial wurde anschließend mit Hilfe der Bildverarbeitungssoftware ImageJ zu einem Bilderstapel zusammengefasst, segmentiert und binarisiert. Die Visualisierung der 3D-Rekonstruktion erfolgte in Matlab®. Der direkte Vergleich der 3D-Rekonstruktion zu den realen Schnittkanten zeigt qualitativ gute Ergebnisse (Abbildung 5).
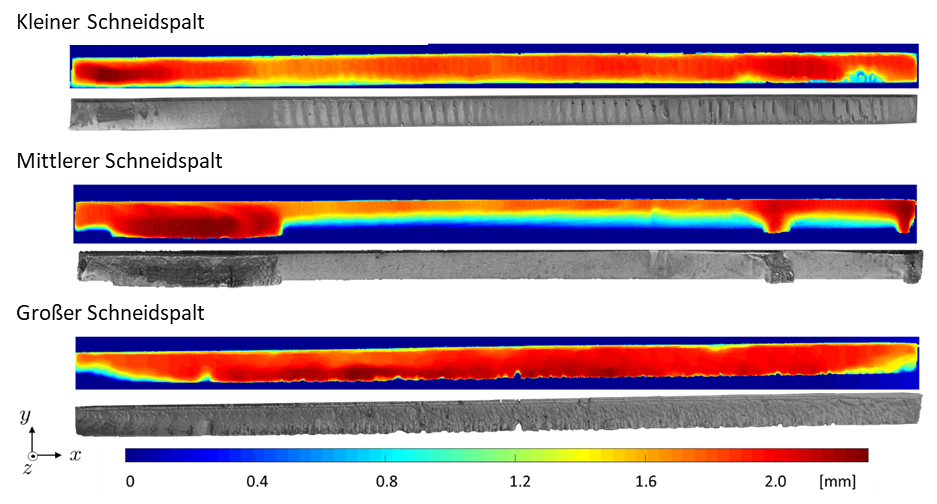